Industrial Computing | Why it’s a Nightmare (Sometimes)
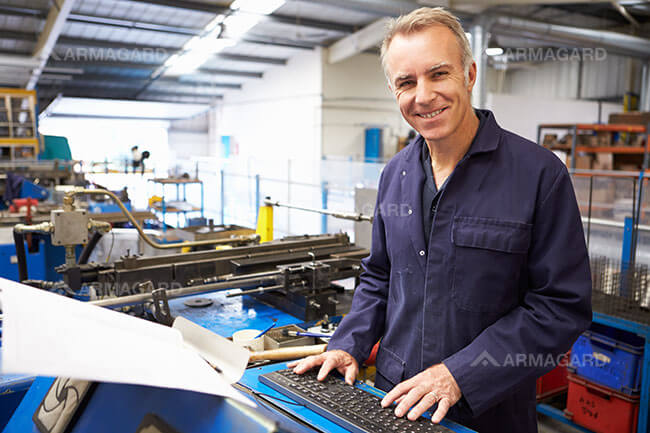
Chances are...you’ve experienced your personal laptop or desktop PC crashing on you before you saved that important document. Hours of work wiped out in an instant, it’s immensely frustrating. Now, take that frustration and multiply it by 10, 100 or even a 1000 and you get an idea of the severity of industrial computing malfunctions.
There’s no doubting that computers have improved the industrial sector immensely. Great strides have been made in efficiency, productivity and the quality of end products, thanks to industrial computing systems.
However, on the odd occasion, computers used in an industrial setting have a tendency to stop working at the most inconvenient moments - usually while you’re trying to complete a massive order.
Let’s face it… it’s not ideal and somewhere in the world right now a computer-controlled systems operator will be shouting expletives at their industrial computer because it has crashed. While a personal PC or laptop crashing loses you a lot of time [and probably makes your blood boil], a simple reboot means you can quickly start over.
With an industrial computing system, it’s not as straightforward and that’s why it’s a nightmare. Most computer systems used in industrial facilities are intricate pieces of equipment that are at the core of production line processes. When they fail, the whole production pipeline grinds to a standstill.
The flaw of industrial computing systems
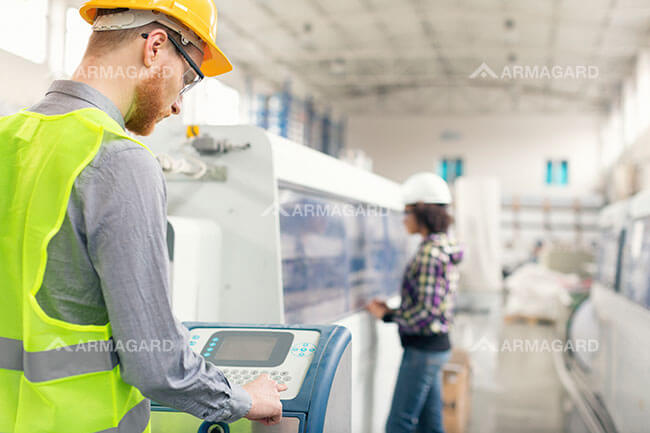
Unfortunately, it’s not a matter of ‘turn it off and turn it back on again’ as the malfunction could be far more problematic than first anticipated. Why? Most industrial computers have all the components rolled into one, i.e. screens, keyboards and other peripherals are not independent of each other. Some would call this convenience.
However, convenience is often costly. So-called ‘all in one’ industrial computing systems are a nightmare because if they fail, getting them up and running again isn’t plain sailing. These systems are designed by manufacturers to the point that only a specialist engineer possesses the knowledge to repair or replace them.
Sadly, once warranties expire or become void, the cost of repair or replacement lies with you and the fees charged are often eye-watering.
Meanwhile, the consequence of having a system that you or any of your personnel can’t fix will lead to an extended period of downtime. Days or even weeks could pass before your industrial computing system is fully functioning again and that downtime will have a dramatic impact on your bottom line.
Unplanned downtime also eats into your lead times. Deadlines are squeezed and you’re operating, minus a crucial computer-controlled system. The knock on effect of failing to deliver a project on time may mean you have to offer a customer discount.
What’s worse is that downtime not only affects one customer, it affects all of your customers as you suddenly have a backlog of orders on your hands.
Meanwhile, failure to deliver at all has far-reaching consequences, not least disgruntled customers, loss of trust, loss of reputation and loss of market share as your customer switches to your competitor. All this because you were counting on a computer system that ultimately failed to withstand the rigours of an industrial setting.
Industrial computing isn’t all bad
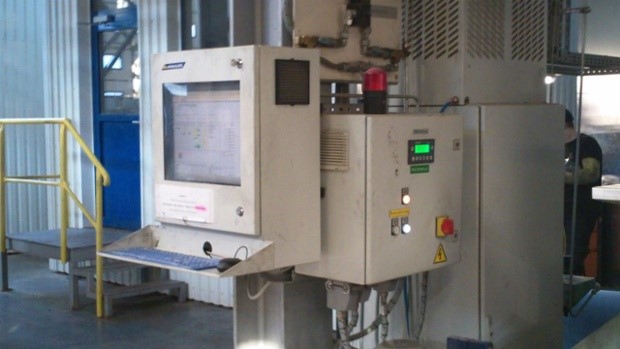
In fairness, incidents of industrial computer failure in a single industrial facility are rare. However, on a collective scale, computer downtime across industrial facilities worldwide means industry as a whole loses millions. In the grand scheme of things, it shows that industrial computer failure has become an epidemic.
For your industrial facility, although rare, two incidents of computer downtime in a year could amount to thousands or even hundreds of thousands in lost revenue, not to mention customer losses. With that in mind, there has to be a better way to reduce computer downtime across industrial facilities, right?
All in one computer systems are great, until they go wrong of course because while you know how to operate them, dealing with any technical problems, repairs or replacements is beyond your own personal expertise.
From a cost perspective, maintenance can be expensive. From a practical perspective, when they do fail, it’s out of your hands. It’s not like you can swap the system out at your own convenience, you’re constantly reliant on an engineer.
Equally, industrial computing systems are always evolving. The second you think you’ve got the latest in industrial computing technology, a new system hits the market. Again, upgrading to the latest system when you’ve just had one installed is no easy feat.
However, there is an alternative, which enables you to swap out and upgrade technologies at your convenience and without having to be tech savvy. Industrial computer enclosures give you the luxury of using standard computer hardware and peripherals such as monitors, PC towers, keyboards, mice and printers in an industrial setting.
With all the durability of a dedicated industrial PC panel, you can setup industrial computing systems that are completely flexible. With each piece of hardware acting as a separate entity, in the event that equipment should fail, you don’t need an engineer to swap out a monitor, a printer or even a keyboard.
Ultimately, this means lower costs, less maintenance and reduced periods of downtime. However, the key benefit is flexibility. Repairs and replacements can quickly be actioned, while upgrading to new technologies is made seamless.
To learn more about manufacturing floor computer integration and the role of industrial PC enclosures, get the guide below…
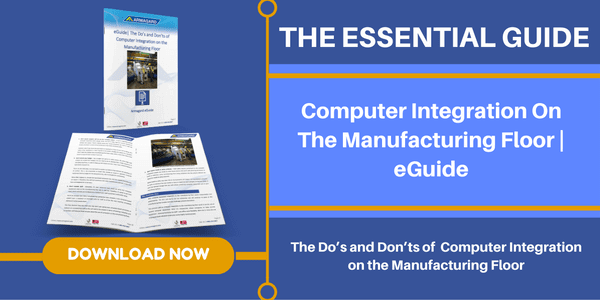