Industrial Computing | 5 Things Computers Hate About Your Manufacturing Floor
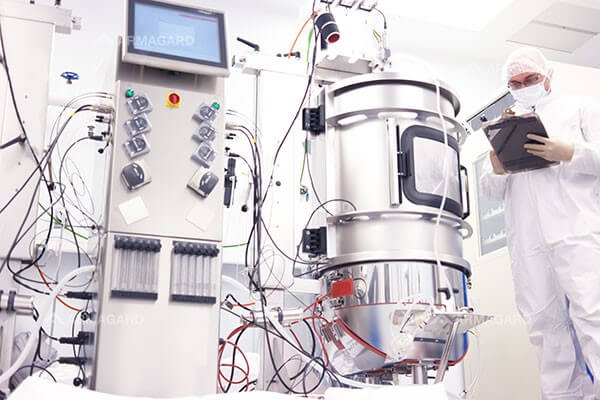
It’s estimated that manufacturing facilities worldwide use at least one computer as part of their operation. However, manufacturers tend to have a love-hate relationship with computer systems. Your manufacturing floor might have some gripes with computers, but here are 5 things computers hate about your manufacturing floor...
Despite their obvious value to your manufacturing floor, computers alone don’t do well in a manufacturing setting – ‘alone’ meaning ‘without any form of protection to enable them to survive in a manufacturing environment.’ This is why there has been a notable increase in IT related downtime incidents across the manufacturing industry.
Computers are notoriously difficult to protect in manufacturing facilities, because there are so many variables. After all, not every manufacturing floor is the same. However, there is one certainty when it comes to computers used in manufacturing, the surrounding environment has an impact on their functionality.
Maybe not today, maybe not tomorrow, but certainly in the near future, computers will succumb to the surrounding manufacturing environment, regardless of what type of facility you’re operating in. Whether you’re in a cleanroom facility or a metal fabrication plant, there’s no escaping the fact that computers need protecting. Here’s why...
The 5 Things Computers Hate About Your Manufacturing Floor
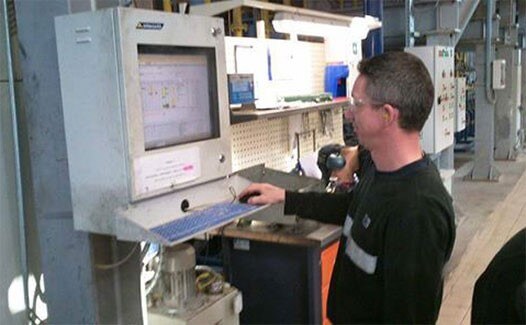
1. Dust — Is the silent computer killer! Although, it’s rife in some manufacturing facilities more than others. Nevertheless, even in cleanrooms where the air is filtered to prevent pollutants like dust getting in, it’s present. Granted it’s present in smaller quantities, but over time those miniscule amounts of dust can build up, especially inside a computer.
That computer quickly becomes a contaminant and your clean room is compromised. Think of it like this, you go to extreme lengths to prevent your cleanroom staff becoming a contaminant, suiting them up in protective clothing. The same principle applies for your facility’s computers.
Protect them, not only to prevent damage to the computer, but to prevent them from becoming a contamination risk.
In harsh facilities, the story is different. It’s more obvious that there are a number of airborne pollutants present that will make the interior of a computer their home. Eventually, dust build up will result in a key component - such as the fans - going kaput.
How Can You Stop Dust Doing Damage?
Whether in a cleanroom or harsh environment scenario, dust has an impact on computer functionality. In the real world a computer system is more likely to fail before you open it up to check for dust build up...
...For this reason alone, computer enclosures are worth having on your manufacturing floor because they eliminate the problem of dust build up. Long-term, you won’t have to worry about damage or contamination.
2. Heat — Computers hate heat in general, but the heat becomes more intense in certain manufacturing facilities, and unprotected computers just can’t cut it in a hot environment.
Computers obviously generate their own heat, which internal fans can dispel. However, add a heat intensive manufacturing facility into the equation, a computer’s own internal fans can’t cope and eventually, the heat will take its toll. Computers need to ‘breathe’ and more importantly, they have to be kept cool.
How Can You Reduce the Impact of Heat?
While encasing a computer in an enclosure may seem counterproductive in terms of reducing the impact of heat, they actually have the opposite effect. Enclosures can be equipped with fans and air conditioning systems to ensure that the internal temperature is optimized to prevent excessive heat.
3. Cold — As with heat, computers don’t work well in sub-zero temperatures. Computer use in cold room manufacturing facilities is becoming increasingly common, but represents a new set of challenges for those manufacturing plants. Not least, how to keep computer components from freezing.
How Can You Use Computers in Freezing Temperatures?
Computer enclosures can be equipped with heating systems to maintain a consistent temperature within the unit that enables computers to fully function in cold environments. This means that computers can be installed in areas such as walk-in freezers.
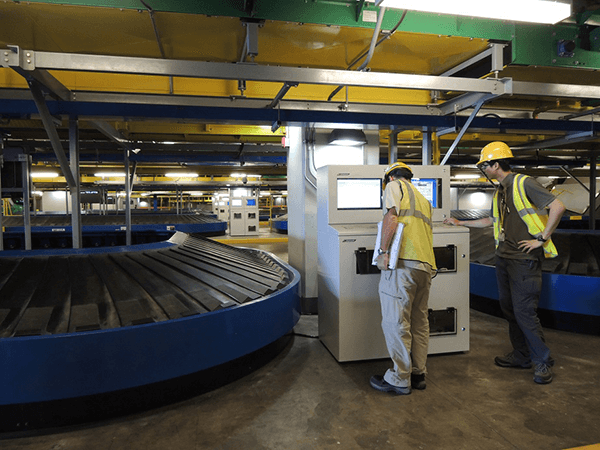
4. Liquids — Some, not all manufacturing facilities use liquids on a day-to-day basis as part of their process, whether it’s water in a washdown facility or paint - as used by paint sprayers. Computers and liquids don’t mix, making the need for protection essential.
What Will Protect Computers From Liquid Damage?
Waterproof computer enclosures are designed to keep out liquids. Whether you work with oils, paints or liquid chemicals, stainless steel enclosures provide the necessary protection for computers used in such environments.
5. People — Last but not least, computers have a love-hate relationship with people. Hate might be too strong a word, but people do take computers for granted. After all, in a manufacturing environment, computers are likely to be used by multiple hands.
They’re bashed, knocked into and it’s not uncommon for the odd cup of tea to be sat on top of the monitor only to be spilt and that puts an end to that computer. To stop your staff getting frustrated with a non-working computer, protection is the best cure.
How Do You Protect Computers from People?
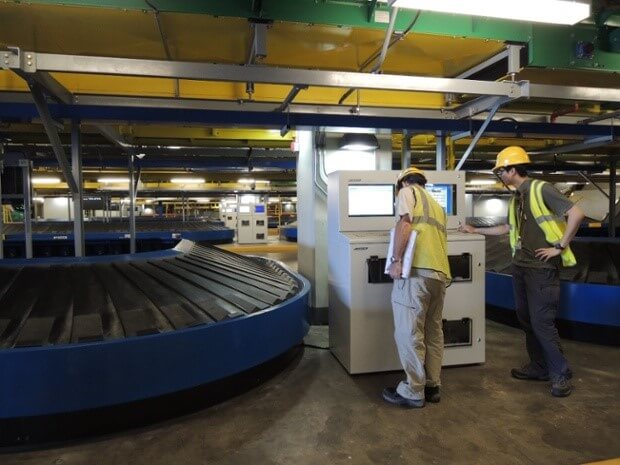
Computer enclosures bear the brunt of impacts likely to be caused by humans. They are the first and last line of defence for any computer equipment used in a manufacturing setting. The hustle and bustle of most manufacturing floors means that the threat of accidental damage from personnel is very real.
Hammering home the point, the use of computers in an ‘out of home’ capacity exposes them to a host of damage threats. In reality, protecting against those things that computers hate about your manufacturing floor is actually more than protecting the computer itself.
In the long-term, the benefits of protecting computer systems on the manufacturing floor are five-fold:
- You’re protecting the production line as a whole.
- You’re dramatically reducing the risk of computer downtime.
- You’re reducing equipment costs in terms of computer repair/replacement.
- You’re safeguarding your reputation by reducing production delays.
- You’re maintaining your market share because you can deliver consistently.
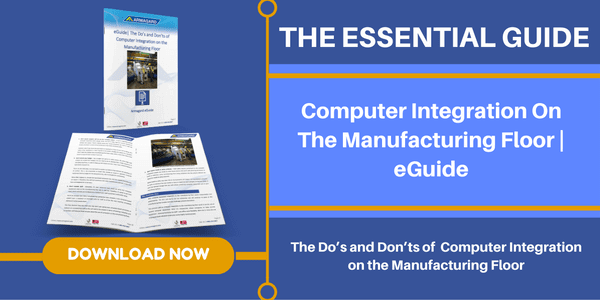