Computer-Integrated Manufacturing (CIM) Explained...Clearly
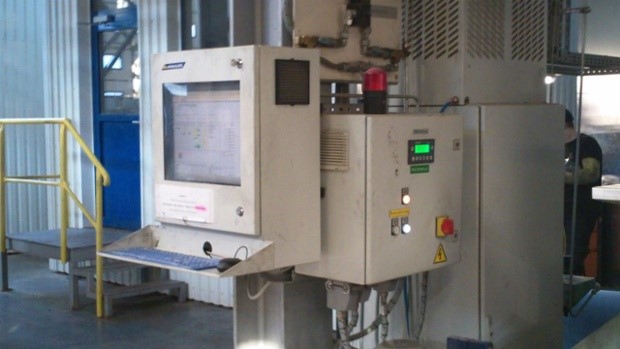
In an era where computers are at the core of production processes worldwide, understanding computer-integrated manufacturing (CIM), and how it can improve operations, is more crucial than ever. In layman’s term, this is CIM explained...
Complex definitions of computer-integrated manufacturing have ‘muddied the waters’ when it comes to understanding what it is and how it can improve production processes. Amid the jargon, it’s easy to lose sight of the benefits that CIM delivers.
What is CIM and how does it work?
In straightforward terms, CIM is the technique of using computers to control an entire production process. It’s commonly used by factories to automate functions such as analysis, cost accounting, design, distribution, inventory control, planning and purchasing.
These functions are often linked to a central, computer-controlled station to enable efficient materials handling and management, while delivering direct control and monitoring of all operations simultaneously. Essentially, every individual piece of a manufacturing process including engineering, production and marketing is organized.
This infographic highlights 10 key functions of CIM:
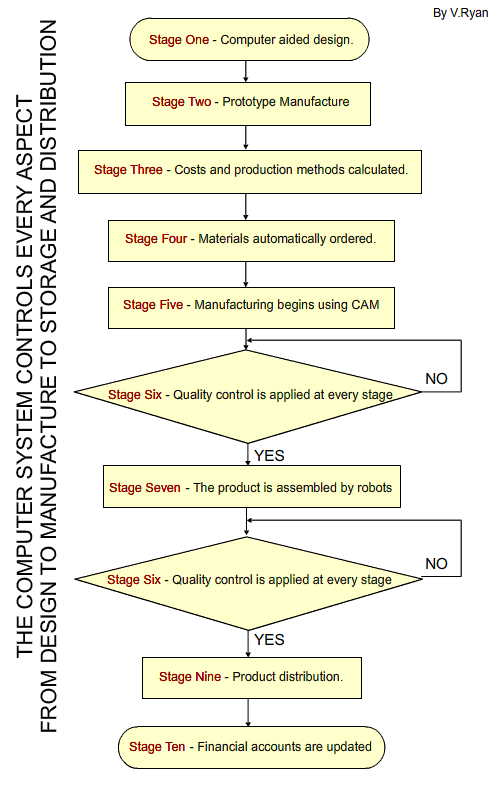
What are the benefits of CIM?
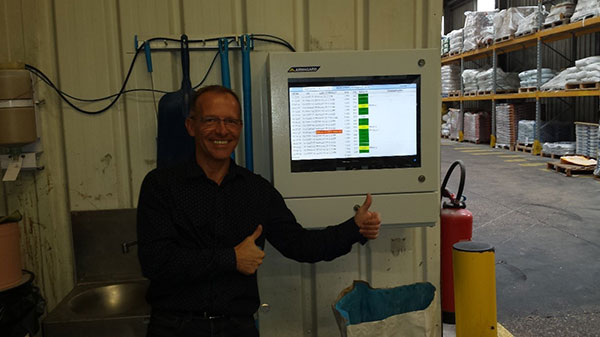
The sole objective of computer-integrated manufacturing is to streamline production processes, delivering the following benefits:
- Reduced costs – i.e. the cost of direct and indirect labour
- Improved scheduling flexibility
- Reduced downtime
- Maintaining correct inventory levels
Ultimately, the goal is to achieve maximum efficiency, closing those gaps that obstruct productivity and result in the bottom-line taking a hit. Additionally, CIM plays a key role in gathering relevant, real-time data from the production floor. For instance, to optimize efficiency, CIM can monitor the operational performance of vital equipment.
Arguably the biggest benefit of CIM is the increase in output capacity it brings. Manufacturing enterprises can go from concept to completion in rapid time, meaning they can produce more in shorter timeframes, which has a positive impact on profitability, customer retention and attracting new customers.
What are the challenges of CIM?
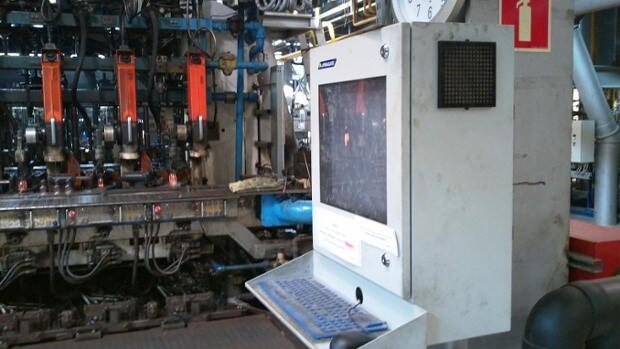
Computers are prone to damage, especially in an industrial setting. The knock on effects of computer failure, for an enterprise that relies solely on computers remaining operational, can be catastrophic and result in:
- Extended periods of downtime
- Idle staff
- Reduced production
- Increased lead times
- Customer dissatisfaction
- Reputational damage
- Loss of market share
When integrated, CIM is responsible for the complete production process. With so much riding on its performance, it’s baffling that many manufacturing firms fail to invest in adequate protection for what is undoubtedly a capital asset.
For instance, specially designed environmental computer enclosures are readily available and exist to protect CIM processes. They are a safe-haven for computers, shielding against external elements such as dust, dirt and liquids and even forklift trucks, just in case ‘Dave’ accidentally reverses into a computer that’s critical to a production operation.
Another key challenge facing CIM is a skills shortage. Many manufacturing firms are lacking skilled-technicians able to operate those systems crucial to CIM. In some quarters, CIM has been slammed for causing jobs losses. In fact, it creates more jobs, but there’s a lack of skills among the current manufacturing workforce, which makes things slightly complicated.
That said, CIM represents an opportunity to upskill the current manufacturing workforce. Ultimately, CIM can benefit manufacturing facilities two-fold:
- By improving the overall production process.
- By improving the skillset of the current workforce.
Considering computer integration on the factory floor? Call +1-866-434-0807 for a no obligation chat, or fill in a contact form to request more information.